Many of the latest engine designs utilize gasoline direct injection systems. But what are they, and how do they work?
The term direct injection seems like a very modern idea, or at least it certainly seems to have become popular in recent years. But the concept itself has been in use for around 100 years in low-pressure form and was once popular with certain car manufacturers in the 1950s. However, direct injection has recently made a return, perhaps most notably with Ford’s EcoBoost range of engines. The reason that these engines are so popular once again (now in more advanced high-pressure form) is for the benefits they offer, which includes hugely improved efficiency and performance over a traditional fuel injection engine. Perfect, then, for some tuning.
How does direction injection work?
As the name suggests, direct fuel injection does exactly what it says on the tin in that the injector sprays directly into the cylinder combustion chamber. But to really understand how that is possible and why it has benefits, it’s important to know how a more traditional manifold or port fuel injection set up works first.
Port fuel injection
As many reading might well know, with this set up a fuel injector sits within the inlet manifold, just before it meets the cylinder head’s inlet ports. It then sprays fuel down into the ports. The engine’s natural induction then carries the fuel to the cylinder’s combustion chamber, where the spark plugs mounted within the cylinder head ignite it.
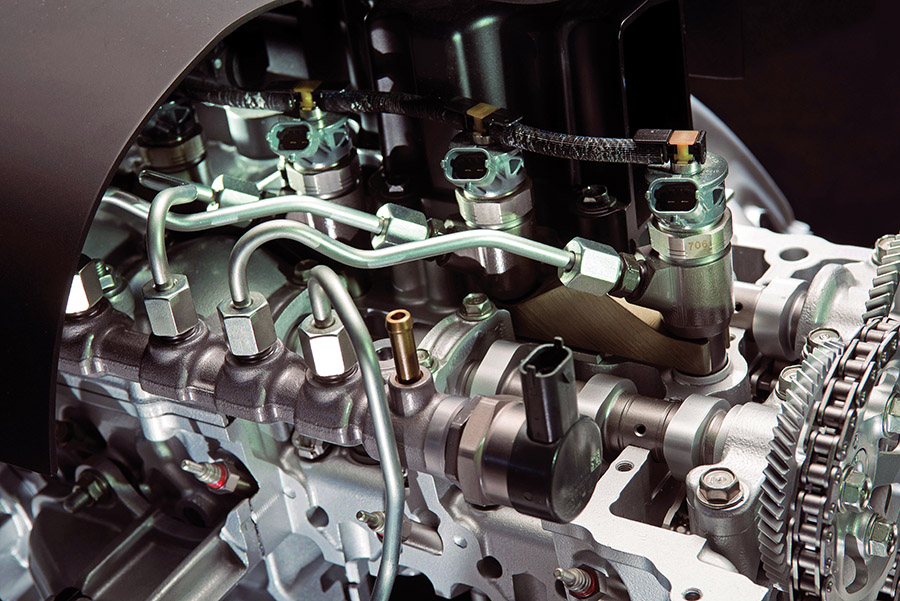
Direct injection systems require high-pressure pumps and injectors to work.
Direct fuel injection
A direct injection set up is far simpler on paper, as the fuel injector is simply mounted within the cylinder head alongside the spark plug, therefore spraying fuel directly into the chamber and cutting out the travelling process. By doing this, you can inject fuel far more carefully and quickly, therefore using less of it and improving efficiency. It also helps to cool cylinder temperatures more effectively, which means there’s a smaller chance of detonation and you can push ignition timing further. This, in turn, creates more power and performance.
However, the system comes with its own complexities. For example, on a Ford EcoBoost engine, the fuel pressure is set to around 220-bar, or around 3,000psi! Whereas, a manifold fuel injection engine would see less than 60psi. As a result of the massively increased pressure, manufacturers need to heavily rework the fuel pump and entire system to cope, using very high-pressure lines and fittings.
The reason for this increased pressure is the length of time the injector has to fire in relation to the spark, as well as the position of the piston in the cylinder. Known as the injector window, on a normal engine this would be around 18-milliseconds, but a direct injection engine has a window to spray fuel of just 6-milliseconds. As it’s so short, the fuel has to be injected very quickly, which is why big capacity injectors are required to work under huge pressure in order to inject large amounts of fuel in a short space of time.
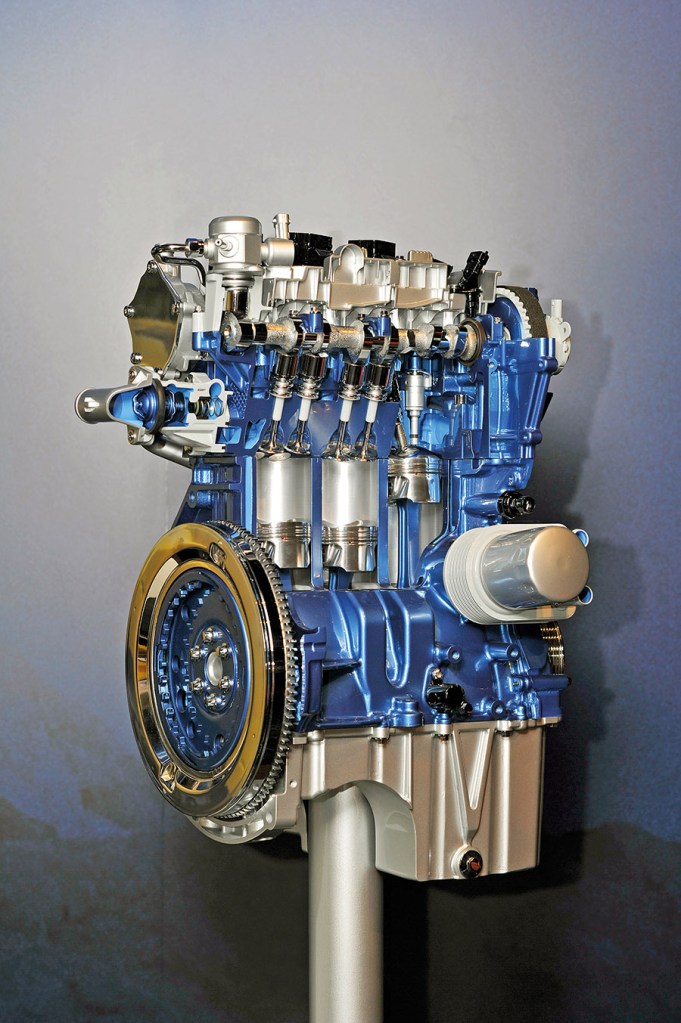
Ford’s award-winning EcoBoost engines use direct injection to maximize performance and efficiency.
Are there any downsides to direct injection engines?
The only real downside to a direct injection set up is that the cylinders contain fuel at all times. That might sound like a positive, but actually it’s not in comparison to a manifold injection set up. That’s because spraying fuel down into the cylinder also happens to do one very important job: it constantly cleans the ports and valves of any oil residue and carbon build up – a particular problem since all engines now need to recirculate any crankcase gases back through the engine to burn them off rather than just vent them to atmosphere as with classic cars.
As a direct injection engine cannot use the fuel injected to clean the inlet tract and backs of the inlet valves, it’s possible to see the ports and valves coke up with deposits, which in time hampers the engine’s efficiency and performance. This occurs slowly over many miles though and there are alternative processes to clean these, and aftermarket upgrades to oil breather systems which will help filter out any oily deposits before recirculating them back through the engine.
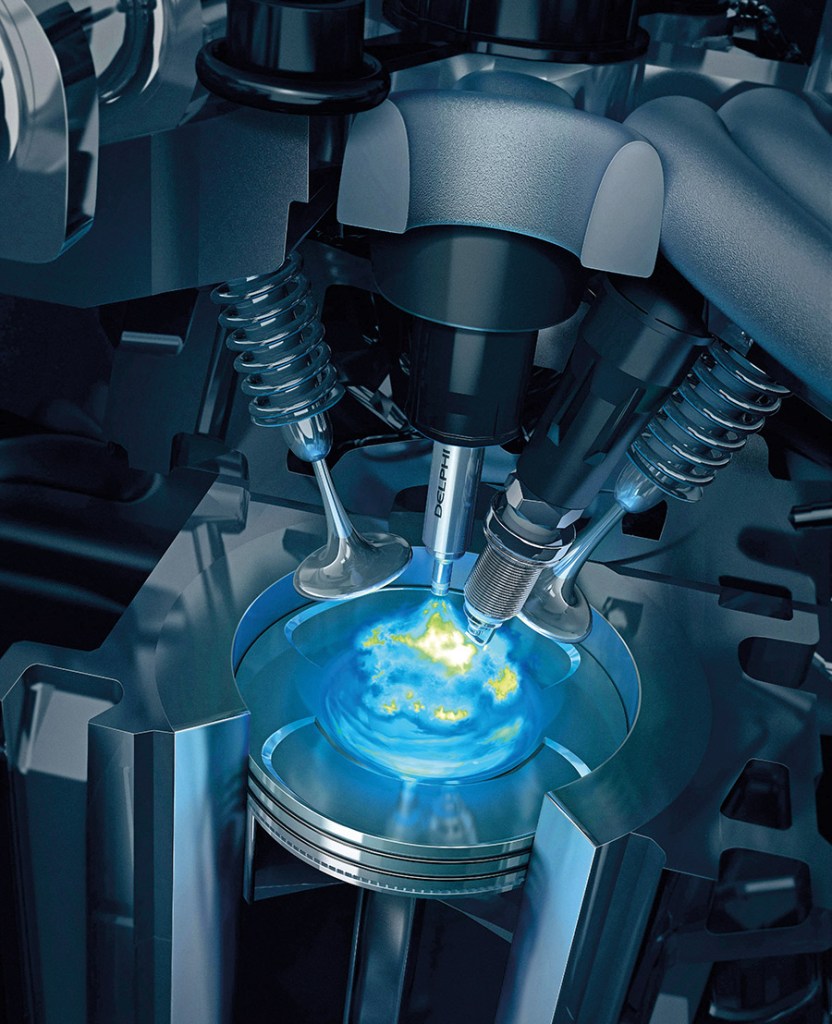
What’s the future of fuel injection?
As you’d expect with today’s drive towards cleaner emissions and more efficient combustion engines, there has been lots of constant development in the field of fuel injection, and one system to keep an eye on is Mahle’s new Jet Ignition system (MJI). This combines port and direct fuel injection systems, with the spark plug and direct fuel injector located within a special pre-chamber above the main combustion chamber.
A small amount of fuel ignites in the pre-chamber, which forces jets of hot, partially-combusted air/fuel through tiny holes in the bottom of the pre-chamber. This then ignites the main air/fuel mix in the main combustion chamber. As a result, the air/fuel mixture ignites more evenly across the whole of the combustion chamber and not just at a single point near the spark plug, making for a more complete combustion, more power, and ultimately better efficiency. If you’re into this kind of thing, check out the Mahle Jet ignition technology.
Words: Simon Holmes